Top-Down Estimating: Definition, Methods, Pros & Cons
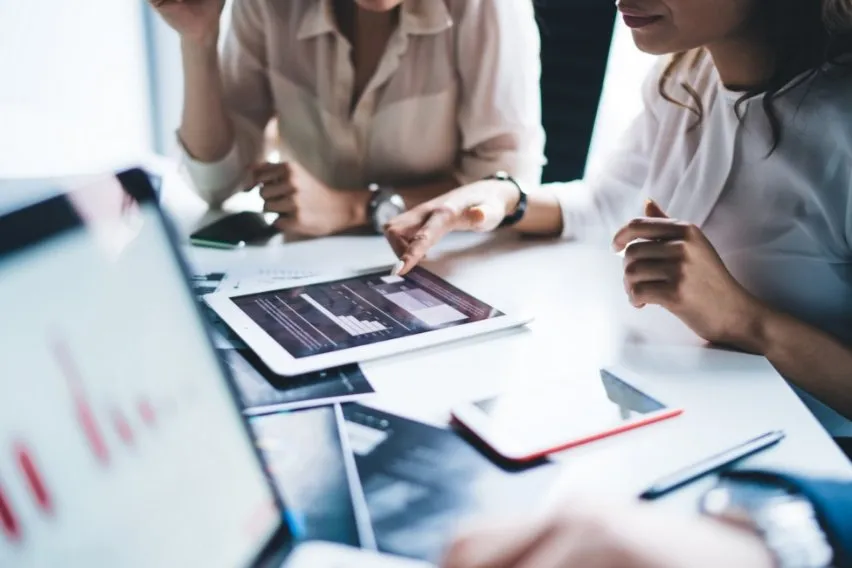
Every successful project starts with a well-crafted plan. One of the most important parts of that plan is understanding the costs involved.
There are many approaches to estimating a project’s cost. Each has its advantages. Each is crucial at different stages in the planning process.
Top-down estimating allows a company’s leadership to increase its decision-making efficiency. Keep reading to learn about this approach and how it differs from other estimation methods.
Table of Contents
Top-Down Estimating Advantages
Top-Down Estimating Disadvantages
Examples of Top-Down Estimating
Top-Down vs Bottom-Up Estimates
What Is Top-Down Estimating?
Top-down estimating is used to create a cost estimate for a project without using detailed information or analysis. It doesn’t list individual prices in granular detail. Instead, it focuses on the budget and general costs for major expenses.
This technique relies on the opinions of experienced managers and data from similar past projects. As a result, it shouldn’t be expected to generate a highly accurate estimate that will align with actual costs during project development.
Instead, it’s used during initial planning to provide guidance on project feasibility. Top-down estimating prioritises efficiency. That’s because it doesn’t need middle management to provide detailed cost breakdowns. This allows project managers to quickly assess potential opportunities. Then they can decide whether to proceed with more detailed estimation methods.
There’s a greater quantity of data to use in the estimation if there are similar projects from the past. This increases the accuracy of the top-down estimate.
Who Uses Top-Down Estimating?
Top-down estimating is often used by company leadership. This includes managers, investors, or other stakeholders.
People in these roles are responsible for smooth projects. They ensure everything aligns with the organisation’s long-term goals. They often use top-down estimates to evaluate potential opportunities or they use them to provide an estimated budget or timeline for a proposed project.
But company leaders are not the only ones involved in the top-down estimating process. It’s possible they don’t understand all the costs related to individual project aspects. So, top-down estimating requires input from lower-level managers or specialists. Staff in these roles often have a better grasp of specific costs and processes.
For example, say a software company wants to expand into a new market. Top-level leadership may first outline the objectives of such a project. Next, they could create a top-down estimate for the projected costs. They would present this estimate to middle managers for feedback. Finally, managers might ask their teams to reveal price estimates for specific items.
Top-Down Estimating Methods
Top-down estimation techniques are often used when conditions are uncertain. As a result, there are different methods of approaching the process. These include:
Consensus Method
The consensus method relieves the responsibility of calculation from a single person. Instead, it takes the estimates of several senior managers into account. These experts use their knowledge and experience to agree on an estimate. The numbers should align with their knowledge of best practices.
Ratio Method
The ratio method uses a key project feature to estimate the total project cost and duration. For example, say a potential construction project’s size is 1,000 square metres. Project managers may use their company’s average cost per metre to estimate the cost of the project. Likewise, knowing the size should help them estimate the completion time.
Apportion Method
The apportion method creates a high-level breakdown of the project’s cost structure. For example, the total project cost would be 100% of the budget. Individual costs are then assigned a percentage of the total project cost. Material costs, for instance, might be 20% of the entire project budget.
This works well when past projects can provide reliable data on features and costs.
Top-Down Estimating Advantages
Top-down estimating has many advantages for business planning and project management. These include:
- Helpful when making initial decisions
Top-down estimating helps teams make quick and informed decisions. Inputting detailed costs and pricing data is unnecessary. So, it’s best suited to big-picture planning.
Top-down estimates provide context. This enables project managers to choose a path forward. Then they can work with other teams to develop more comprehensive plans.
- Flexible estimates
Top-down estimates are created with the understanding that the estimates are adjustable. The editing process happens over time as more information becomes available.
This approach allows for more flexibility with smaller-scale decisions. It’s especially helpful for projects that don’t require knowledge of every factor up front.
- Requires less effort than other estimating techniques
Top-down estimating requires less time and effort than other estimating techniques. It’s best used for quick decision-making.
It’s also great for choosing between several opportunities. It’s a valuable approach when one doesn’t have access to all the project specifications or pricing data.
Top-Down Estimating Disadvantages
Top-down estimating isn’t without its drawbacks. There are some disadvantages to the approach to be aware of, including:
- Discrepancies with actual project cost
Top-down estimates can vary wildly compared to the actual project costs. This happens because of a lack of detailed analysis. A company should prepare itself for the possibility of significantly overshooting the initial budget.
- Relies on assumptions
Most top-down estimates rely on historical data and the project manager’s experience. As a result, the final assessment will include assumptions that may be inaccurate.
So, when using the top-down approach, use reliable data as much as possible.
- A top-heavy approach may lead to inaccuracies
Top-down estimates are often conducted by senior management within the company. This contrasts with bottom-up estimates, which collect information from every organisational level.
Sometimes a project manager will not have enough knowledge about specific costs. This means the top-down estimate will likely be inaccurate.
Examples of Top-Down Estimating
Top-down estimating is common across all industries. Below are examples of how the approach may apply to construction/technology development.
- Construction Projects
When constructing a new building, companies often use top-down estimating to get a sense of the tentative budget. This doesn’t serve as the final plan. Still, a top-down estimate is useful for determining potential costs.
For example, a project manager can use their knowledge of similar projects to estimate costs for the new building. These may include the price of materials in that region, labour cost, or land price. After finalising more details, the company can revisit the top-down estimate. Then they can revise it with more accurate information.
- Software Development
Technology companies can use the top-down approach to check a project’s feasibility. This technique applies to hardware, like laptops, and software, like mobile apps.
Suppose a company decides to expand operations by launching a personal finance application. They might first create a top-down estimate of potential costs. Doing so will determine if the app fits the company’s strategic plans.
Next, technical specialists may provide input on the costs of feature development. They might also provide insight into user acquisition. Once the top-down estimate is complete, they can decide whether to proceed with the planning process.
Top-Down vs Bottom-Up Estimates
There are different approaches to generating project estimates. Each method has its merits. Project managers should use the method most suitable for their planning stage.
Top-down estimating is a quick way to come up with approximate project costs. In contrast, the bottom-up approach prioritises detail. That makes top-down estimating more useful during the initial planning stages. Bottom-up estimating provides a more comprehensive view. So, it’s more useful further on in the planning process.
Project managers use top-down estimating when the project has the following characteristics:
- In the initial planning stage
- High uncertainty
- Unstable scope and timeline
- Flexible budget without fixed-price contracts
- Internal, rather than involving external stakeholders
Bottom-up estimating may be more appropriate when a project has these attributes:
- Further along in the planning stages
- A need to minimise risk and uncertainty
- Stakeholders that need a high level of detail
- A restricted budget
- High similarity to past projects
- A high degree of collaboration between internal teams
Key Takeaways
Top-down estimating helps project managers make high-level decisions based on general project feasibility. It takes less time and effort than other estimating methods. That’s because it relies on historical data and experience rather than detailed analysis.
Estimating accurate project details is crucial when it comes to project planning. Without a good estimate, a company may not dedicate enough resources to the project. So, estimates directly impact the project’s outcome and success.
Project managers craft reliable top-down estimates. And for this, there are many dedicated software tools on the market. But the software is only as good as the data. It’s crucial to use reliable historical data. This will complement the experience from similar projects in the past.
FAQs on Top-Down Estimating
What is a characteristic of top-down estimating?
Top-down estimating is less rigorous than other estimation techniques. It allows decision-makers to choose which projects to pursue. It also gives them an idea of the costs involved.
What is an alternative to top-down estimating?
One alternative to top-down estimating is bottom-up estimating. It breaks the estimate down into the deliverables at each level. It does this by focusing on accurate costs and timelines for each item. It’s a more precise estimation method but requires more time and effort to produce.
Is analogous estimating the same as top-down?
Top-down estimating is also referred to as analogous estimating. It’s a method that relies on presently available information rather than taking a detailed, bottom-up approach.
Is parametric estimating top-down?
Parametric estimating combines the use of historical data in top-down estimating with the increased accuracy of bottom-up estimating. This method applies a formula or algorithm to scale the historical data points. For example, suppose a past project took eight weeks to complete and cost $10,000. Parametric estimating uses these data points as inputs when calculating costs for a new project.
RELATED ARTICLES