What Are Standard Costs? They’re Estimates
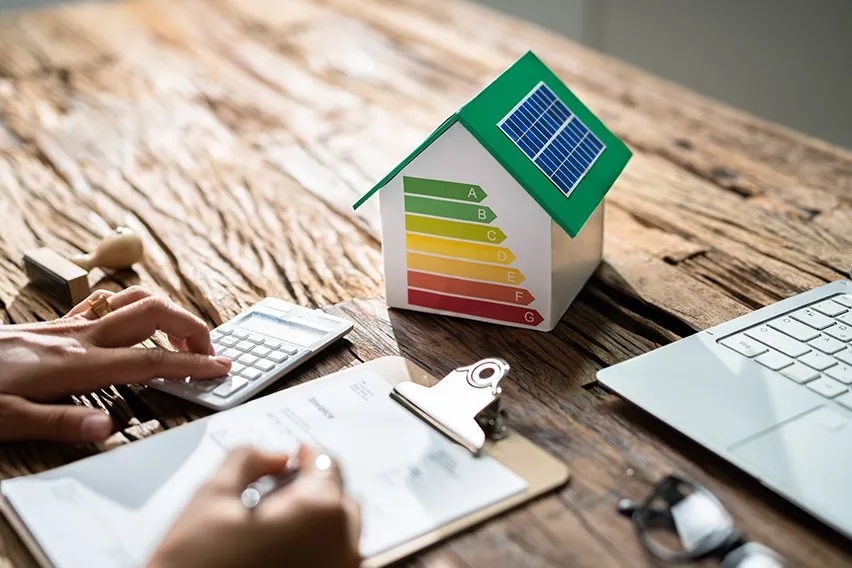
Standard costs are estimates of the actual costs in a company’s production process, because actual costs cannot be known in advance. This helps a business to plan a budget. Later, when the actual costs are determined, the company can see if it has a favorable budget variance (meaning, actual costs did not exceed standard costs) or unfavorable budget variance (the standard costs were exceeded).
Here’s What We’ll Cover:
Why Do Companies Use Standard Costs?
How Do You Calculate Standard Cost?
Standard Costing Disadvantages
Is a Standard Cost Different from a Budget?
NOTE: FreshBooks Support team members are not certified income tax or accounting professionals and cannot provide advice in these areas, outside of supporting questions about FreshBooks. If you need income tax advice please contact an accountant in your area.
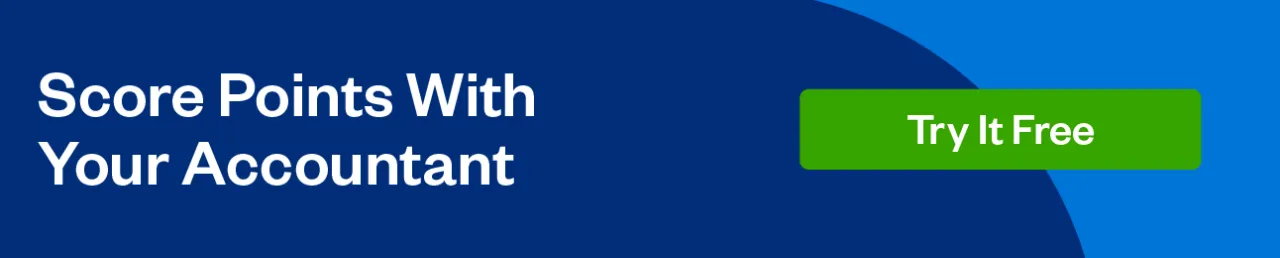
Why Do Companies Use Standard Costs?
Companies use standard costs for budgeting because the actual costs cannot yet be determined. This is because in the manufacturing process, it is impossible to predict the demand of a product or all the variables that will affect the costs of manufacturing it.
This does not mean the actual costs will never be used, typically a company’s accountant will periodically update the variances as that information becomes available.
Standard costs not only help a company to budget for their expenses but to establish prices for their products.
Standard costs are also known as “pre-set costs”, “predetermined costs” and “expected costs”.
At the end of the year (or accounting period) if the standard costs are higher than the actual expenses, than the company is considered to have a favorable variance. If the company’s actual costs were higher, then the company would have an unfavorable variance. These variances can be drilled down to find specifically where in the manufacturing process the actual cost differences lie between standard and actual; for instance, labor cost variances, material cost variances, etc.
For more on favorable and unfavorable variances, please consult “What Is a Favorable Variance?”
How Do You Calculate Standard Cost?
To calculate the standard cost of a product, a company must do the following:
Standard Cost Formula
Standard Cost = Direct Labor + Direct Materials + Manufacturing Overhead
Direct Labor Calculation
Direct Labor = Hourly Rate x Hours Worked
Direct Materials Calculation
Direct Materials = Raw Materials x Market Price
Manufacturing Overhead Calculation
Manufacturing Overhead = Fixed Salary + (Machine hours x Machine rate)
With the exception of the hourly rates, all of these numbers will need to be estimated.
Standard Costing Advantages
There are a number of benefits to using the standard costing technique. Standard costing:
Allows a Company to Budget
A budget for a company (that manufactures a product) cannot be prepared without standard costing. When a dollar amount is assigned to labor, materials and manufacturing overhead, the budget can be completed.
A budget is always an estimate, later compared to the actual amounts spent, so that the creation of the following year’s budget is more accurate. In this way, assuming there are not significant product or manufacturing changes year after year, the sizes of the variances can decrease.
Means A Company Can Assign a Value to Its Inventory
All a company needs to do to calculate its inventory value is to multiply the amount of actual inventory by the standard cost of each item. Because it’s the “standard” cost being used in the calculation, the number won’t be dead on accurate, but it’s likely to be close to the actual cost if the company has been doing a similar type of production for a while.
Calculating inventory using standard costs is easier than using actual costs. This is because in reality, one batch of a product may cost more to produce than another batch of the exact same product. Maybe there were production delays on the line resulting in staff overtime to finish that second batch. Imagine these types of problems happening all the time, making it very difficult to keep track of the actuals.
Yes, eventually those extra charges will be accounted for by being added to the variance cost, but typically an inventory valuation will go by the standard costing method in order to keep things simplified.
Makes It Possible for a Company to Set a Product Price
Without the information standard costing provides, it would be impossible to set a price for a product. This is because that price is in part calculated on the costs involved in manufacturing that product (including labor, materials and overhead costs).
Allows Financial Records to Be Produced Easier and Faster
Taking the time to continuously update actual costs means a lot of number adjustments for a company’s accountant. Standard costs assumes there are no fluctuations in prices. As a result, the required financial reports for a company’s management can be generated easier and faster.
Allows for Benchmarking
The standard costs associated for a company’s products allows management to set benchmarks, so that the actual costs can eventually be compared. If the benchmarks are met, that’s great. If not, and there is an unfavorable variance, then the company can try to determine efficiencies in the production process to lower those costs in the future.
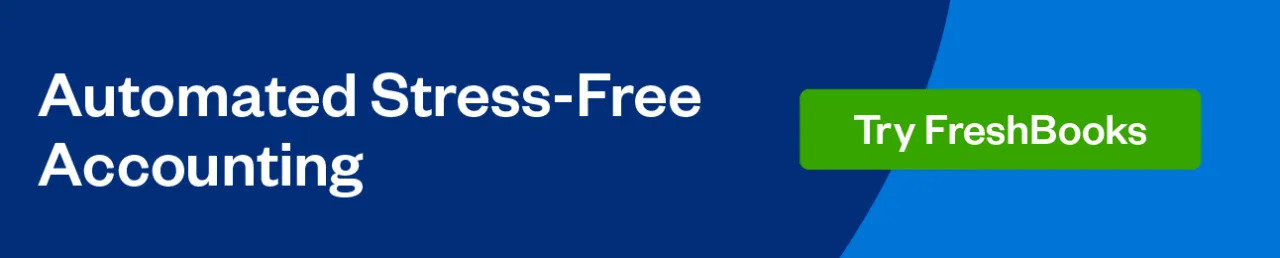
Standard Costing Disadvantages
There are disadvantages to standard costing as well. Standard Costing:
Assumes Little Change to the Estimated Costs
The standard costing method assumes there will be little changes in the budgeted amounts in the foreseeable future. However, if a product is unexpectantly discontinued or a new one introduced, or there are new efficiencies or deficiencies in the production process, this can result in significant variances from the estimates.
Often Doesn’t Provide Enough Information to Distinguish Product Units
If a company has a very complex manufacturing system, with multiple items being produced, it is often impossible to single out the standard costs for one product unit. Analyzing a product unit can help a company determine its value, however, it would need to be done using actual costs as opposed to standard costs.
Focuses on Unfavorable Variances
Often favorable variances are not noted at all, and unfavorable variances are scrutinized. This can lead to some problems with staff, as often the production process, including how labor is used, is reassessed when unfavorable variances arise. Staff may feel their performance is being questioned, when it’s possible that the estimates may have been too low in the first place, and that the line already runs efficiently.
Is a Standard Cost Different from a Budget?
A standard cost is not the same as a budget.
A budget is an estimate of expenditures for a specific accounting period, typically a quarter or year. Standard costs are estimates used for totals in some of the line items in that budget, as they related to manufacturing costs.
RELATED ARTICLES